Мировой опыт применения стальной и полипропиленовой фибры при строительстве туннелей
- Эдуард Бычков
- 22 сент. 2018 г.
- 4 мин. чтения
Часть Первая.
Контракт 250.
Подрядчик – Nuttall, Wayss & Freytag/Kier Joint Venture.
Железнодорожное сообщение в туннеле под Ла-Маншем (CTRL) - первая новая магистраль железной дороги, построенной в Великобритании за последнее столетие. Ее строили двумя секциями, которые соединили туннель под Ла-Маншем со станцией St.Pancras Station в Лондоне. Секция 1 соединила туннель под Ла-Маншем с магистралью железной дороги в северном Кенте и секция 2 соединила туннель под Темзой и продолжилась под восточной частью Лондона до станции St. Pancras Station. Существовали 4 контракта по секции 2 CTRL. По всем этим контрактам сдвоенная внутренняя облицовка туннеля диаметром 7.15м была произведена прямо на строительной площадке. Один из контрактов по Лондонской секции – Контракт 250, Ripple Lane to Barrington Road.
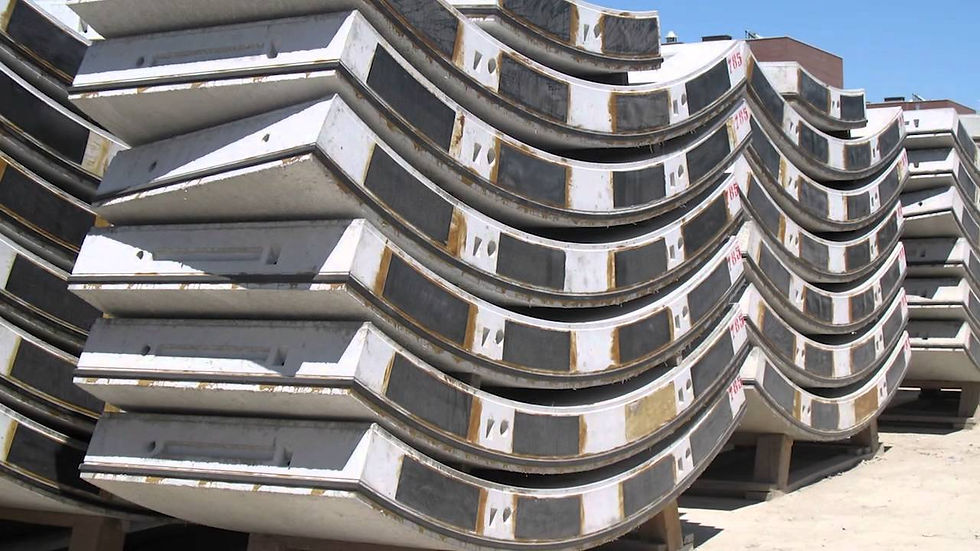
Сборные сегменты.
Контракт 250 был выигран совместным предприятием Edmund Nuttal, Wayss & Freytag and Kier Construction и состоял из 530-метрового участка незавершенного туннеля, который должен соединить сдвоенные 5,3 – километровые туннели от Dagenham на запад к Stratford. В дополнение, там есть одна вентиляционная шахта, соединенные вентиляционные каналы и 7 поперечных каналов, соединяющих эти два главных туннеля, приблизительно по 700 метров длиной каждый. Контракт был оценен в сумму около 130 млн. фунтов стерлингов и туннели прокладывались двумя туннелестроительными машинами западнее от Ripple Lane в Dagenham. Туннели были обделаны сборными сталефибробетонными сегментами с внутренним диаметром 7150мм и толщиной 350мм. Сегменты собирались в кольцо шириной 1,5м, состоящее из 10 сегментов (См. рисунок 1). Сегменты длиной 2,5 метра соединены 24 мм болтами ввинченные в специально отлитые углубления сегмента.
Производство сегментов.
Было принято решение произвести необходимые 70000 сегментов, каждый из которых весит приблизительно 3.2 тонны, на строительном участке. Это позволило избежать затрат на транспортировку приблизительно 225000 тонн сегментов автомобильной или железной дорогой от отдаленного участка. Сегменты были изготовлены в традиционной статической форме, один сегмент в день от каждой формы. Был возведен специальных цех общей площадью 7750m2 , в котором были размещены 210 форм, производящих 21 кольцо в день и в среднем 100 колец в пятидневную неделю. Шесть цеховых кранов и специальные грузоподъемные механизмы обслуживали цех. Четверть закрытой площади была необходима, чтобы сегменты набирали проектную прочность в закрытом помещении в течение трех дней прежде, чем их переместят на складской двор (См. рисунок 2)
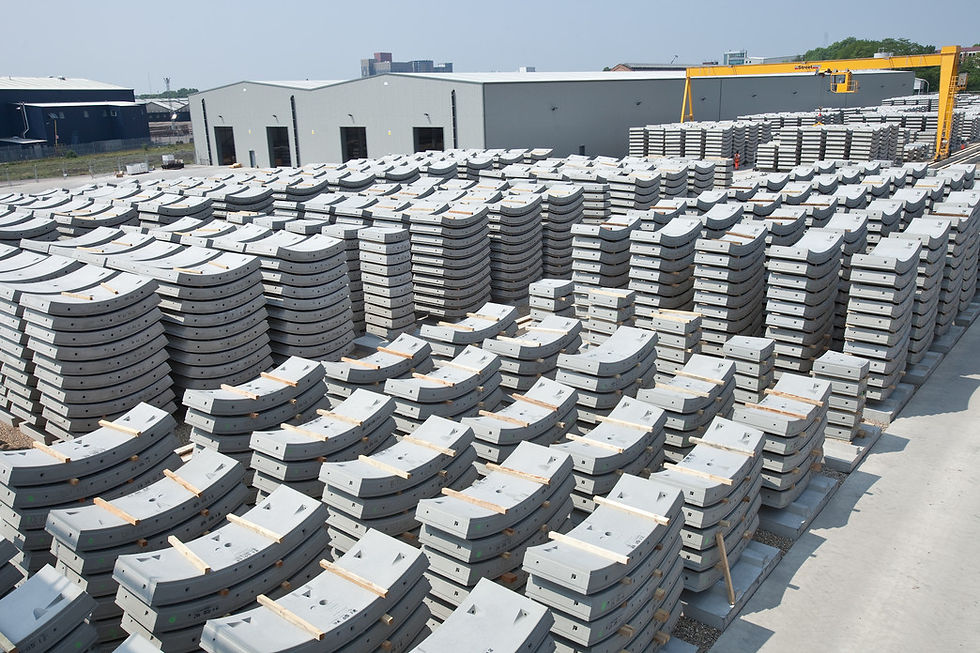
Часть Вторая.
Формы для сегментов.
Размерная точность требовала следующие допуски + - 1 мм по ширине, +-2mm по толщине, +-0.5mm на углублениях герметизирующих прокладок вокруг сегмента и 0,1mm по периметру радиальных швов. Эта точность может быть достигнута только со статическими формами. Таким образом, полностью механизированные стальные статические формы, вместе с двумя внешними вибраторами, были произведены компанией CBE(Франция) - специализированной компанией по изготовлению форм, у которой есть опыт в изготовлении форм с необходимой точностью (См. рисунки 3 и 4)
Состав бетонной смеси.
Состав бетонной смеси был результатом опыта, приобретенного во время строительства Туннеля под Ла-Маншем и Юбилей Лайн, вместе с анализом пожара, случившемся в Туннеле под Ла-Маншем. Требование высокой долговечности и низкой себестоимости с хорошей сопротивляемостью к огню привело к конкретной спецификации по прочности на сжатие 60MPa, содержащей щебеночные или гранитные заполнители, Стальные армирующие фибры с расходом 30 кг/м3, чтобы увеличить предел прочности и 1кг/м3 Фибры полипропиленовой, чтобы предотвратить взрывное откалывание бетона в условиях огня. После многократных испытаний и исследований был установлен следующий состав бетонной смеси: 1.Обычный портландцемент - 287 кг/м3 2.Зола уноса - 123kg/m3. (BS 3892-1:1997 Зола уноса. Спецификация для золы уноса при использовании с портландцементом). 3.Песок - 514 кг/м3 4.Щебеночный заполнитель 10 мм - 684 кг/м3 5.Щебеночный заполнитель 20 мм - 643 кг/м3 6.Фибра стальная - 32.5 кг/м3 (50x1-миллиметровые) 7.Фибра полипропиленовая - 1 кг/м3 8.Суперпластификатор - 2 литра 9.Максимальное водоцементное соотношение - 0.36 10.Фактора уплотнения - 0.93
Тестирование бетона.
Очень строгое тестирование качества бетонной смеси проводилось через каждые 100м3, тесты на уплотняемость через каждые 20м3. Также проводилось еженедельное тестирование прочности на изгиб.
Производство бетона.
Бетон поставлялся из бетонного завода, который был построен прямо на строительной площадке – модифицированный Steelfields Major SM60 с 3м3 планетарным миксером. Заполнитель подавался по конвейеру из пяти 50-тонных бункеров, цемент из двух 35-тонных силосов и зола уноса из 60-тонного силоса. В дополнении был возведен специальный узел для дозирования стальной и полипропиленовой фибры. И стальная и полипропиленовая фибра поставлялись специализированными производителями этих материалов. Удобоукладываемость бетонной смеси строго контролировалась специальными сенсорами. Бетонный завод при эксплуатационной производительности в 60м3 бетона в час производил только 35 м3 в час, так как этого было вполне достаточно для того, чтобы произвести требуемые 250м3 бетона в день для дневного цикла заливки.
Цикл заливки.
Заливку изделий производили обычно с 6 часов утра до 6 часов вечера, после чего изделия оставляли в форме и они набирали прочность при управляемых условиях в течение следующих 12 часов. После этого изделия освобождали из формы и перемещали в зону хранения на территории фабрики до определенного срока, в зависимости от окружающих температур. Чтобы избежать теплового шока, основные и поверхностные температуры изделий сверялись с окружающей температурой. Когда дифференциал температур становился удовлетворительным, изделия были перемещены во внешний склад, способный к хранению 25000 сегментов общим весом приблизительно 76000 тонн, где они были штабелированы по десять изделий на специальных бетонных опорах (См. рисунок 5)
Часть Третья.
Выводы.
Такая организация процесса позволила до начала работ по устройству туннеля иметь на площадке готовой продукции на три месяца работы туннелестроительных машин. Все это позволило сократить сроки строительства. (См. рисунок 6)
Применение стальной и полипропиленовой фибры также позволило сократить время для производства бетонных сегментов, сократить трудозатраты и сэкономить на материалах, так как вместо арматурных каркасов применялась только фибра (стальная и полипропиленовая) в указанных выше пропорциях.
Contract 250. По материалам Британского Сообщества Бетона Concrete Society. Перевод сделан компанией Concrete Global UK Limited, Великобритания. Данный переводной материал является собственностью компании Concrete Global UK Limited. При использовании данного материала просьба указывать источник получения с указанием названия компании Concrete Global UK Limited.
Comentários